
Introduction
For pet food processors and manufacturers, the landscape is evolving rapidly. Ensuring the safety and consistency of products is not merely a goal; it is a fundamental requirement in an industry under intense scrutiny from consumers and regulatory bodies alike. Production Managers, Plant Managers, and QA/QC professionals are on the front lines of this challenge daily. The precise application of all ingredients, including essential vitamins and minerals, is paramount. Failures in this area can lead to significant negative consequences, as recent industry events have demonstrated. The use of advanced solutions such as AutoJet® Precision Spray Systems is becoming increasingly vital in addressing these demands and mitigating such risks.
Quick Takeaways
- Enhance Pet Food Safety & Quality: AutoJet® Precision Spray Systems ensure accurate, uniform application of additives, including vitamins, which is critical for product consistency, nutritional accuracy, and safety.
- Reduce Costly Ingredient Waste: Minimize the overuse of expensive palatants, vitamins, and mold inhibitors with precise spray control, directly impacting the bottom line.
- Achieve Regulatory Compliance: Consistently meet stringent FDA regulations and AAFCO standards for pet food production through accurate dosing and verifiable processes, preventing issues such as excessive vitamin levels.
- Boost Operational Efficiency: Experience less downtime from cleaning and maintenance due to reduced overspray, leading to optimized throughput and higher Overall Equipment Effectiveness (OEE).
- Improve Product Palatability & Nutrition: Ensure consistent kibble coating for enhanced taste appeal and precise delivery of vitamins and minerals for nutritional accuracy with AutoJet® Precision Spray Systems.
- Safer Work Environment: Drastically cut down on airborne mist and overspray of additives, creating a cleaner, safer workspace for employees.
- Customizable & Data-Driven Solutions: Tailor AutoJet® systems to specific production needs and leverage data logging for continuous process improvement and quality assurance in pet food manufacturing.
The Growing Challenge: Ensuring Safety and Consistency in Pet Food Production
For pet food processors and manufacturers, the landscape is evolving rapidly. Ensuring the safety and consistency of products is not merely a goal; it is a fundamental requirement in an industry under intense scrutiny. Production Managers, Plant Managers, and QA/QC professionals are on the front lines of this challenge daily.
Rising Consumer Expectations and Regulatory Scrutiny (FDA, AAFCO)
Today’s pet owners are more informed and discerning than ever before. They demand transparency and high-quality ingredients, pushing for nutritional accuracy and safety assurances. This heightened consumer awareness is mirrored by stringent regulatory bodies such as the Food and Drug Administration (FDA) and the Association of American Feed Control Officials (AAFCO). These organizations continuously update and enforce standards, meaning that achieving and maintaining AAFCO compliance spray technology and adhering to FDA regulations pet food production is paramount. It is not just about avoiding penalties; it is about building and maintaining consumer trust. A key insight here is that proactive compliance and transparent communication about quality control processes can become a significant brand differentiator, turning regulatory obligations into a competitive advantage. Recent legal actions within the industry underscore the critical importance of adhering to these established nutrient level guidelines.
The High Cost of Inaccuracy: Recalls, Reputation, and Revenue
Inaccuracy in pet food production, particularly in the application of critical additives such as vitamins, carries a hefty price tag. A product recall, whether due to excessive levels of certain vitamins, as highlighted in recent lawsuits, or insufficient application of preservatives, can lead to staggering financial losses. Consider the implications if a batch of kibble is produced with vitamin levels that significantly exceed AAFCO maximums. If this leads to product recall and legal challenges, the direct costs include product retrieval, disposal, and replacement. However, the indirect costs—damage to the brand’s reputation, loss of consumer confidence, and subsequent decline in revenue—can be far more devastating and long-lasting. This underscores the importance of precision at every step, especially when dealing with ingredients like vitamin D that have narrow tolerance levels and can be harmful in excess. The ripple effect of a single significant recall or widely publicized lawsuit can impact market share for years, a risk that proactive quality control measures, including advanced spray systems engineered for precise dosing, aim to mitigate.
Common Pain Points in Additive Application (Vitamins, Palatants, Mold Inhibitors)
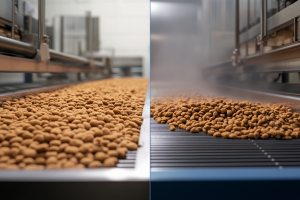
Engineering and Maintenance Managers are likely familiar with the operational headaches caused by suboptimal additive application. Common pain points include uneven coating, leading to inconsistent product performance, and the over-application or under-application of crucial ingredients. For example, vitamins must be applied with utmost precision; too little, and the nutritional claims are not met; too much, and there is a risk of toxicity, potentially leading to regulatory non-compliance and legal action. Palatants are essential for product acceptance, but if not applied uniformly, one bag of food might be devoured while another from the same batch is ignored by pets. This inconsistency can lead to customer complaints and erode brand loyalty. Similarly, the effectiveness of mold inhibitors hinges on even distribution to enhance pet food shelf life and prevent spoilage. Traditional spraying methods often struggle with these nuances, leading to clogged nozzles, excessive misting, and significant ingredient waste in pet food. These challenges highlight the need for solutions like AutoJet® Precision Spray Systems to achieve consistent, accurate results, especially for critical micronutrients with defined AAFCO limits.
What are AutoJet® Precision Spray Control (PSC) Systems?
Understanding the technology behind solving these production challenges is key for Plant Managers and Engineering teams. AutoJet® Precision Spray Control (PSC) Systems, developed by Spraying Systems Co., represent a significant advancement from conventional spraying methods, offering a sophisticated approach to applying liquids, including vital micronutrients, in pet food manufacturing.
Core Technology: Precise Application, Minimal Waste
The core principle of AutoJet® Precision Spray Systems lies in their ability to deliver an exact, repeatable amount of liquid precisely where it is needed. This is achieved through advanced control technology that synchronizes spray output with production line variables, such as conveyor speed or product presence. Imagine applying a concentrated vitamin solution where AAFCO guidelines dictate very specific minimum and maximum levels; the system ensures that the correct dosage is applied to the kibble, minimizing the risk of exceeding safe limits. This precision additive spraying minimizes overspray and can help reduce the costly waste of ingredients, while critically supporting compliance with established nutritional standards. A key insight here is that this level of control not only saves direct costs but also contributes to a cleaner operating environment, less frequent cleanup, and, most importantly, a safer, more consistent product.
Key Components: Nozzles, Manifolds, and Automated Control
Several key components work in concert within an AutoJet® system. At the heart are high-speed, electrically actuated spray nozzles, such as PulsaJet® nozzles, which can cycle on and off thousands of times per minute. This rapid cycling allows for extremely fine control over flow rate without altering spray pressure, ensuring consistent droplet size and coverage. These nozzles are typically mounted on custom-engineered manifolds, ensuring optimal positioning and spray angle for the specific application. The entire process is governed by an automated spray controller. This controller is the brain of the system, managing spray timing, flow rates, and often integrating with existing plant control systems. For a QA/QC Manager, this means verifiable and repeatable application, crucial for consistent product quality and adherence to AAFCO compliance spray technology for all additives, including vitamins.
How PSC Differs from Traditional Spraying Methods
Traditional spraying methods often rely on continuous spraying or rudimentary on/off controls, which can lead to significant inefficiencies and inaccuracies in dosing. For instance, conventional systems might use pressure changes to control flow rate, which unfortunately also alters spray angle and droplet size, leading to inconsistent coverage, inconsistent kibble coating, and potential for over- or under-application of critical ingredients. Overspray is common, resulting in wasted additives and a potentially hazardous work environment due to misting. In contrast, Precision Spray Control (PSC) technology, as found in AutoJet® Precision Spray Systems, uses high-speed cycling of nozzles while maintaining constant liquid pressure. This means the spray pattern and droplet size remain optimal, regardless of line speed changes or the need for intermittent spraying, facilitating accurate dosing of even small-volume additives. A Production Manager will appreciate this because it translates to less product rejection, minimized ingredient waste in pet food, a more predictable, reliable coating process, and critically, a reduced risk of exceeding safe additive levels. This precise control also makes it easier to help reduce cross-contamination in pet food manufacturing by containing the spray within the target area.
Key Benefits of AutoJet® Systems for Pet Food Manufacturers
For pet food manufacturers, from Production Managers to Executives and Business Owners, the adoption of advanced technology such as AutoJet® Precision Spray Systems translates into tangible benefits that address key operational, financial, and regulatory goals. These systems are not just an equipment upgrade; they are a strategic investment in quality, safety, and efficiency.
Enhanced Product Quality and Consistency: Uniform Additive Distribution
One of the most significant advantages is the marked improvement in product quality and consistency. AutoJet® Precision Spray Systems ensure uniform additive distribution, which is crucial for achieving consistent kibble coating and accurate nutrient levels. Whether it is a palatant to ensure pets find the taste appealing or a specific vitamin blend for nutritional accuracy, even coverage means every piece of kibble meets exact specifications. For QA/QC Managers, this translates to fewer deviations from quality standards, greater confidence in the final product, and a robust system for maintaining compliance with AAFCO and FDA guidelines for nutrient content. This consistency is a cornerstone of brand trust and customer satisfaction, directly impacting repeat purchases.
Improved Food Safety: Accurate Dosing, Reduced Contamination Risk
Food safety is non-negotiable, extending to the precise levels of all ingredients. AutoJet® systems contribute directly to safer products through accurate dosing of all applied liquids. This precision is vital for ingredients like mold inhibitors, where thorough coverage is needed, or vitamins, where over-application could lead to toxicity and regulatory non-compliance (as seen in instances like excessive Vitamin D levels), directly impacting FDA regulations pet food production and AAFCO standards. Furthermore, by minimizing overspray and misting, these systems help reduce cross-contamination pet food manufacturing risks between different product runs or incompatible ingredients. This precise application means a safer product for pets and a more compliant operation for the plant.
Significant Cost Reduction: Minimized Waste of Expensive Coatings & Additives
The financial benefits are compelling. By applying coatings and additives with exceptional accuracy, AutoJet® Precision Spray Systems significantly help minimize ingredient waste in pet food. Expensive palatants, vitamins, and mold inhibitors are applied only where needed and in the precise amounts required. A Plant Manager will quickly see the impact on the bottom line as the cost of wasted raw materials plummets. A less obvious, yet substantial saving, comes from reduced rework and fewer rejected batches, directly improving overall manufacturing profitability.
Increased Efficiency: Reduced Downtime and Optimized Throughput
Operational efficiency sees a boost with AutoJet® systems. The precision application reduces the need for frequent cleanups caused by overspray and misting. Furthermore, the reliability and automation of these systems mean less downtime associated with manual adjustments or equipment malfunctions often seen in older spray technologies. For an Engineering or Maintenance Manager, this translates to more predictable maintenance schedules and higher overall equipment effectiveness (OEE). Optimized throughput becomes achievable as the coating process becomes a more reliable and consistent part of the production line.
Better Worker Safety: Reduced Misting and Overspray Hazards
Creating a safer environment for employees is a critical responsibility. Traditional spray systems can generate significant airborne mist and overspray, which can create slip hazards and expose workers to concentrated additives. AutoJet® Precision Spray Systems are engineered to minimize these issues. The targeted spray and reduced atomization mean less aerosolization of liquids, leading to cleaner air and a safer workspace. This is a crucial benefit that contributes to overall employee well-being and can reduce risks of workplace incidents, a concern for any conscientious Production Manager or Business Owner.
Applications of AutoJet® Systems in Pet Food Processing
The versatility of AutoJet® Precision Spray Systems makes them invaluable across various stages of pet food processing. For Plant and Production Managers, understanding these applications can reveal opportunities to enhance product characteristics, ensure nutritional accuracy, and improve operational efficiency. These systems offer solutions for the accurate delivery of a wide array of liquid additives, ensuring the final product meets the high standards customers and regulatory bodies demand.
Precise Application of Palatants for Enhanced Appeal
Palatability is a critical factor in the pet food world. If pets do not like the taste, the nutritional value becomes irrelevant. AutoJet® Precision Spray Systems excel at precision palatant spraying. By ensuring each piece of kibble receives a consistent, uniform coating of liquid or powder palatants (when slurried), manufacturers can significantly improve the appeal of their product. This accurate application avoids both wasteful over-coating and unappetizing under-coating, leading to a more consistent and desirable product for pets. Ensuring every batch achieves the same high level of palatability can lead to greater customer satisfaction and brand loyalty.
Uniform Coating of Vitamins and Minerals for Nutritional Accuracy
Nutritional accuracy is critical for meeting label claims, ensuring pet health, and complying with regulatory standards such as AAFCO guidelines, which set minimum and maximum levels for nutrients like Vitamin D. Vitamin application systems in pet food must be exceptionally precise to prevent both deficiency and toxicity. AutoJet® systems provide the necessary control to apply vitamins and minerals uniformly and accurately, ensuring that each serving of pet food delivers the intended and safe nutritional value. This helps manufacturers meet stringent AAFCO compliance spray technology guidelines and avoid issues related to nutrient imbalances, which can lead to product recalls and legal challenges. For QA/QC Managers, the ability to reliably and consistently apply these vital micronutrients is a cornerstone of product integrity and risk management.
Effective Spraying of Mold Inhibitors for Extended Shelf Life
Shelf life is a major concern for both manufacturers and consumers. Mold inhibitor spray systems for pet food play a crucial role in preventing spoilage and maintaining product safety over time. AutoJet® systems ensure that mold inhibitors are evenly distributed across the product surface, providing comprehensive protection. This effective application helps to enhance pet food shelf life, reduce waste due to spoilage, and maintain product quality from the plant to the consumer’s home. This is a practical way to safeguard the product and brand reputation.
Application of Release Agents to Prevent Sticking and Improve Flow
In the production process itself, efficiency can be hampered by products sticking to equipment. Release agent spray systems in pet food manufacturing, when powered by AutoJet® technology, can precisely apply thin, even layers of release agents to conveyors, dies, and other surfaces. This prevents buildup, reduces cleaning downtime, and ensures a smoother, more continuous production flow. For an Engineering Manager, this means less wear and tear on equipment and more uptime.
Other Additives: Antioxidants, Colorings, and More
The utility of AutoJet® Precision Spray Systems does not end there. These systems are also highly effective for applying a range of other additives, such as antioxidants to prevent fat rancidity, natural or approved colorings for product differentiation and consumer appeal, and even liquid probiotics. The precise control offered by these systems ensures that these often costly or sensitive ingredients are applied efficiently and effectively, contributing to the overall quality, safety, and appeal of the final pet food product while helping to minimize ingredient waste in pet food.
Integrating AutoJet® Systems into Your Existing Production Line
For many pet food manufacturers, the thought of integrating new technology can seem daunting, potentially raising concerns about disruption and compatibility. However, AutoJet® Precision Spray Systems from Spraying Systems Co. are engineered with practical integration in mind, aiming to enhance, not overhaul, existing operations. This focus on seamless adoption is crucial for Plant Managers and Engineering/Maintenance Managers tasked with overseeing such upgrades.
Customizable Solutions for Various Production Scales
Whether for a boutique pet food producer or a large-scale manufacturing facility, there is no one-size-fits-all solution. Recognizing this, AutoJet® Precision Spray Systems offer a high degree of customization. Systems can be tailored to accommodate different line speeds, product types (kibble, treats, etc.), and the specific additives being applied, such as those for consistent kibble coating or precise vitamin dosing. Spraying Systems Co. works with clients to design manifolds, select appropriate nozzle types (like PulsaJet® for precise, intermittent spraying), and configure controllers to match unique production environments. This ensures that the implemented system is perfectly suited to capacity and operational needs, making it an effective pet food safety automation tool.
Ease of Integration and Maintenance Considerations
Integrating AutoJet® systems is generally a streamlined process. The modular design of many components allows for flexible installation, often requiring minimal modification to existing production lines. Controllers can typically interface with current plant automation systems, allowing for centralized monitoring and control. From a maintenance perspective, which is a key concern for Engineering/Maintenance Managers, these systems are built for durability and ease of service. Features like self-cleaning nozzles or quick-change nozzle assemblies can reduce downtime. A key insight is that the precision of these systems often leads to a cleaner spraying environment, which in turn can reduce the maintenance burden on surrounding equipment by minimizing buildup of sticky or corrosive additives.
Data Logging and Process Verification Capabilities
In today’s data-driven manufacturing environment, process verification is essential for quality assurance, compliance, and risk mitigation. Many AutoJet® Precision Spray Systems offer sophisticated data logging capabilities. This means QA/QC Managers can track key spray parameters, such as flow rates, duty cycle, and liquid pressure, for each batch. This data provides an auditable record of the coating process, which is invaluable for demonstrating compliance with FDA regulations pet food production and AAFCO guidelines regarding nutrient levels. If an issue, such as an incorrect vitamin dosage, does arise, this historical data can be critical for root cause analysis and swift corrective action. Furthermore, these logs can be used to optimize spray parameters over time, ensuring continuous improvement in application efficiency, product consistency, and adherence to safety standards. This moves beyond simple application to intelligent process control, helping to minimize ingredient waste in pet food and ensure product safety through ongoing optimization.
Choosing the Right AutoJet® System for Your Needs
Selecting the optimal AutoJet® Precision Spray System is a critical decision that can significantly impact a pet food production’s efficiency, quality, regulatory compliance, and profitability. It is not just about purchasing equipment; it is about finding a tailored solution that addresses specific challenges, such as the precise application of vitamins within AAFCO limits, and helps achieve strategic goals. This process involves careful assessment and expert consultation, ensuring that Executives, Plant Managers, and Engineering teams are aligned.
Assessing Your Current Challenges and Goals
The first step is a thorough evaluation of current operations. What are your primary pain points? Are there struggles with inconsistent kibble coating, excessive waste of expensive additives like palatants or vitamins, or difficulties meeting AAFCO compliance spray technology standards, including precise vitamin D levels? Perhaps the goal is to enhance pet food shelf life through more effective mold inhibitor application or to improve improving pet food palatability consistently. Clearly defining challenges—such as issues with current vitamin application systems pet food, the risk of exceeding safe nutrient levels, or the need to reduce cross-contamination pet food manufacturing—and setting measurable objectives will guide the selection process. For example, if the primary concern is ingredient cost and regulatory compliance for critical additives, the focus might be on a system that maximizes transfer efficiency and dosing accuracy for the specific coating.
Consulting with Spraying Systems Co. Experts
Navigating the range of available spray technologies and configurations can be complex. This is where partnering with specialists becomes invaluable. Spraying Systems Co. pet food solutions are backed by decades of expertise in spray technology across numerous industries. Their engineers can provide an on-site assessment or lab testing to understand unique application requirements, including the viscosity of liquids, the desired droplet size, the characteristics of the production line, and critical dosing parameters for sensitive ingredients. They can help quantify the potential ROI by analyzing potential reductions in ingredient waste, improvements in production efficiency, and enhanced compliance. This consultative approach ensures investment in an AutoJet® Precision Spray System that is truly optimized for specific needs, rather than a generic solution.
Real-World Success Stories in Pet Food Manufacturing (Case Studies)
Seeing is believing. Learning about how other pet food manufacturers have successfully implemented AutoJet® Precision Spray Systems can provide powerful insights and build confidence in the technology. Spraying Systems Co. often has case studies available that detail the challenges faced by other companies, the specific AutoJet® solution implemented, and the quantifiable results achieved. These might showcase improvements in pet food coating accuracy, reductions in the use of expensive palatants through precision palatant spraying, or enhanced safety and accuracy in applying vitamins and mold inhibitors. These real-world examples can help visualize the potential impact on operations and provide a benchmark for what can be achieved. A valuable insight from these case studies is often the unexpected ancillary benefits, such as reduced cleaning downtime or improved employee morale due to a cleaner work environment, that go beyond the primary objectives of cost saving and quality improvement.
Frequently Asked Questions
Q: How do AutoJet® Precision Spray Systems help meet pet food safety regulations like those from the FDA and AAFCO, particularly concerning vitamin levels?
A: AutoJet® Precision Spray Systems enhance pet food safety by ensuring highly accurate and uniform dosing of critical additives such as vitamins (e.g., Vitamin D) and mold inhibitors. This precision is crucial for manufacturers to comply with FDA regulations and AAFCO standards, which often stipulate specific minimum and maximum allowable nutrient levels. Accurate application prevents over-application, which can lead to toxicity and regulatory action, and under-application, which can compromise nutritional value or shelf life. This helps reduce contamination risks and ensures the final product meets all safety and nutritional guidelines.
Q: What is the primary advantage of AutoJet® Precision Spray Systems over traditional spraying for coating kibble?
A: The primary advantage of AutoJet® Precision Spray Systems is their use of Precision Spray Control (PSC). Unlike traditional methods that alter pressure and thus spray patterns and droplet size, PSC uses high-speed, electrically actuated nozzles to deliver a consistent droplet size and precise application. This minimizes overspray and prevents inconsistent kibble coating, regardless of line speed changes, which is critical for uniform additive distribution.
Q: How can AutoJet® Precision Spray Systems lead to cost savings in pet food manufacturing?
A: AutoJet® Precision Spray Systems significantly help minimize ingredient waste in pet food by applying expensive coatings, palatants, and vitamins directly and accurately onto the product. This precision palatant spraying and additive application reduces overspray, meaning less product is wasted on equipment or in the air, leading to substantial cost reductions in raw materials.
Q: What are key applications where AutoJet® Precision Spray Systems enhance pet food quality and consistency?
A: AutoJet® systems are used for precise application of palatants to improve taste, uniform and accurate coating of vitamins and minerals for nutritional integrity within regulatory limits, and effective spraying of mold inhibitors to enhance pet food shelf life. These applications ensure a consistent, high-quality, and safe product that meets both consumer expectations and regulatory requirements.
Q: Do AutoJet® Precision Spray Systems improve safety for workers in pet food plants?
A: Yes, AutoJet® Precision Spray Systems contribute to better worker safety by significantly reducing airborne misting and overspray of additives. This leads to cleaner air in the plant, fewer slip hazards from wet surfaces, and minimized worker exposure to potentially irritating or concentrated liquid ingredients, creating a safer overall work environment.
Conclusion
In the demanding landscape of pet food production, ensuring safety, quality, and consistency is paramount. AutoJet® Precision Spray Systems emerge as a crucial technology for manufacturers aiming to meet and exceed these expectations. By delivering precise and uniform application of vital additives like palatants, vitamins (within specified AAFCO and FDA limits), and mold inhibitors, these systems directly enhance final product quality, ensuring consistent nutritional value, heightened palatability, and, critically, product safety. This precision not only helps in achieving AAFCO compliance and adhering to stringent FDA regulations but also significantly minimizes the costly waste of expensive ingredients and can help reduce the risk of product recalls and associated legal actions stemming from issues like excessive vitamin levels.
For Production Managers, QA/QC professionals, and Plant Executives, investing in AutoJet® technology translates to tangible operational benefits. Beyond substantial cost savings from reduced additive consumption and less rework, these systems can improve overall equipment effectiveness by minimizing downtime associated with cleaning and maintenance. Furthermore, the reduction in overspray and misting contributes to a safer working environment. AutoJet® Precision Spray Systems are more than an equipment upgrade; they are a strategic investment in operational excellence, brand reputation, product safety, and sustainable profitability. To discover how these advanced spray solutions can be customized to address specific production challenges and elevate quality control, consider consulting with spray technology experts to explore the optimal AutoJet® system for your facility.
Leave a Reply